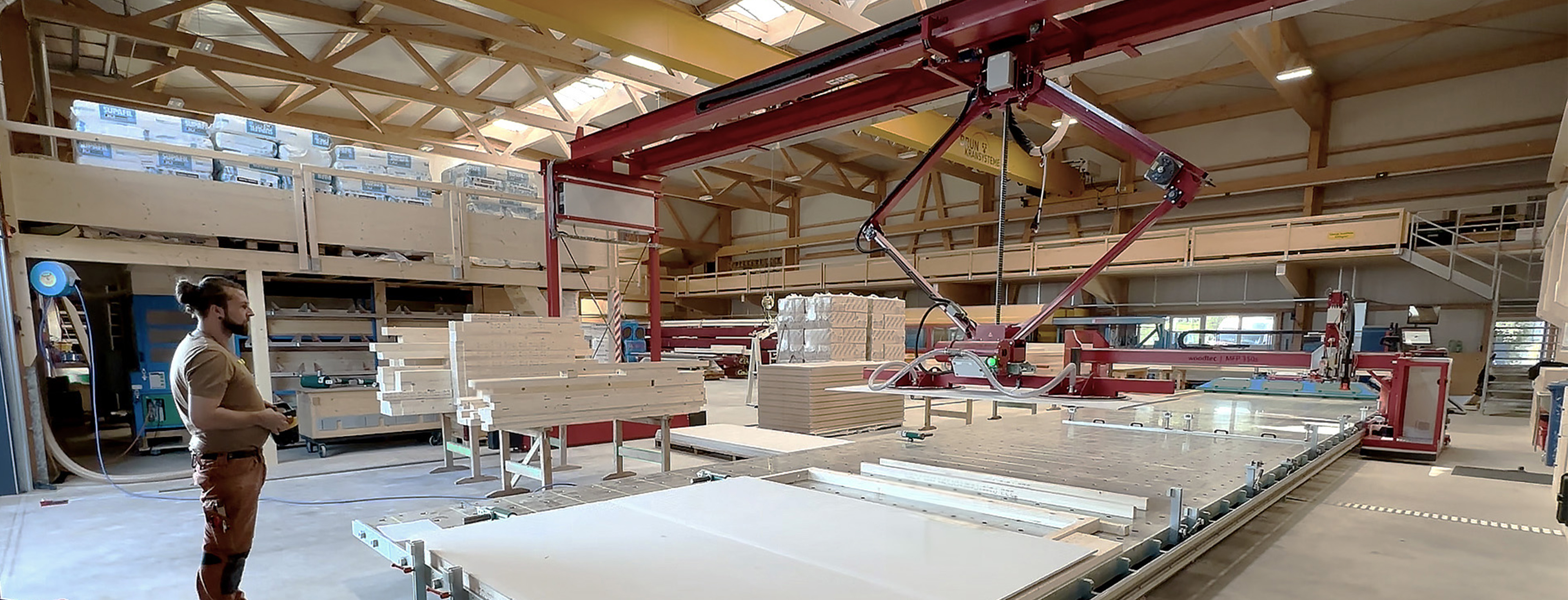
Maschinentechnik für alle Arbeitsschritte
Um Fachkräften weiterhin spannende Arbeitsplätze bieten zu können und die Mitarbeiter gleichzeitig zu entlasten, hat die Graz SA aus dem schweizerischen Lausanne über die
letzten Jahre die Maschinentechnik in der Vorfertigung schrittweise ausgebaut. Dieser Ausbau war nicht nur risikoarm, er erlaubte auch genau die Prozesse zu optimieren, bei denen Engpässe entstanden waren, und die Produktivitätssteigerungen genau zu verfolgen und zu lenken.
Das familiengeführte Unternehmen Graz SA wurde 1988 gegründet und befindet sich mit den Brüdern Jonathan und Fabien Graz in der Hand der zweiten Generation. Das Unternehmen aus Lausanne auf der Schweizer Seite des Genfer Sees beschäftigt 15–20 Mitarbeiter und ist im Holzbau breit aufgestellt: von mehrgeschossigem Wohnungsbau über Schulen und Verwaltungsgebäude
bis hin zu Renovationen und Umbauten.
Hundegger für Abbund, woodtec für
Vormontage
Die Fertigungshalle wurde 2014 im Bestreben gebaut, den Holzrahmenbau und die Vorfertigung als neues Standbein auszubauen.
Aufgrund der Anforderungen an Flexibilität bei den Projekten und Präzision bei deren Ausführung entschloss man sich dazu, eine eigene Abbundanlage von Hundegger anzuschaffen. Die gleichen Überlegungen bewogen das Unternehmen 2016 zur Anschaffung von Montagetischen von woodtec Fankhauser. „Unser Ziel war, die Vorfertigung zu beschleunigen und die Präzision der Elemente zu steigern“, erklärt der Zimmermeister und aktuelle Geschäftsführer Jonathan Graz, warum man sich damals für woodtec entschied. „Der Tisch wurde von Leuten entworfen, die selbst usprünglich Zimmerer waren.“
Ebenfalls in die Waage fielen die Vielseitigkeit des Tisches und der darauf herstellbaren Elemente, zahlreiches Zubehör, um die verschiedensten Arbeitsschritte zu rationaliseren, und die Erweiterungs- und Ausbaumöglichkeiten.
Ausbau zur Montageplattform für die Montage der Rähme
Aufbauend auf einem 12-m-Montagetisch, wurden über die Jahre und mit steigender Projektzahl zusätzliche Module hinzugefügt, sodass der Tisch nun eine 18 m lange Plattform bietet, die sehr indiviuell und je nach Projekt und Elementen in einzelne Arbeitsstationen unterteilt werden kann. In der Regel werden bei Graz drei Elemente nebeneinander gefertigt. „Wir haben die Fertigungsanlage aber so ausgelegt, dass wir bei steigendem Bedarf noch bis auf 21 m ausbauen können“, erklärt Graz. Die Kompaktheit der Anlage ist nicht nur wegen der engen Platzverhältnisse ein Vorteil und reduziert die Platzmiete, sondern relativiert auch die Anschaffungskosten durch optimierte Auslastung. Manchmal geht im Zuge der Automation die Montage der Rähme, die auf allen Anlagen nach wie vor händisch erfolgt, etwas unter. Sie macht aber nach Schätzungen bis zu 50 % der Produktionszeit aus. Je nach Wahl des geeigneten Montagetisches kann man dort ohne große Automation sehr viel an Produktivität gewinnen oder verlieren, meint Graz.
Dächer, Decken und verleimte
Kastenelemente
Einen weiteren Entwicklungsschritt machte das Unternehmens im Jahr 2021 mit der Herstellung von verleimten Kastenelementen. Standardmäßig bietet der Montagetisch zusätzliche Erweiterungen, um Dächer und Decken traditionell zu fertigen, die auch bei Graz in Einsatz kamen. Neu dazu kommt aber die Erweiterungsmöglichkeit um eine sogenannte Pressvorrichtung, die das Verkleben von Kastenelementen auf demselben Tisch ermöglicht.
Bei einem Schulgebäude konnte man die Ingenieure von den Vorzügen von Kastenelementen überzeugen und deren sachgerechte Herstellung dank der Anlage von woodtec garantieren.
„Das hat den Anstoß dazu gegeben, in diese zusätzliche Erweiterung zu investieren“, erklärt Graz den Effekt eines ersten Prototyps. „Heute bieten wir viele Geschossdecken und Dächer in geklebter Ausführung an.“ Die verbesserte Statik, tolle Sichtflächen ohne Schrauben und die Möglichkeit, Einbauhöhe zu gewinnen, überzeugen die Kunden.
Materialhandling
Der nächste Ausbauschritt kam 2023 mit der Anschaffung eines Handlingkran Pro von woodtec. „Wir mussten unbedingt eine Lösung für das Handling der Materialien finden“, erklärt Graz. „Der Hallenkran war ständig besetzt, und es entstanden damit teure Wartezeiten in der Produktion.“ Auf die Frage, welche Alternativen man ins Auge gefasst hatte, nennt Graz einen zweiten Brückenkran. Aber das wäre statisch auf der Bahn nicht möglich und auch von den Platzverhältnissen her nicht ideal gewesen, da die beiden Brücken nicht kreuzen können. Schlauchheber respektive Säulenschwenkkräne waren keine realistische Option, da sie von der Traglast her den Hallenkran nicht entlastet hätten. Zudem wäre man im Einsatzbereich zu eingeschränkt gewesen und hätte mehrere Kräne benötigt. Das wäre in puncto Invest einem Handlingkran Pro nahe gekommen, hätte aber technisch viel weniger Möglichkeiten geboten.
Alle Arbeitsschritte optimiert
Die neue Fertigungsanlage bei Graz SA
Ein Teleskopkran für verschiedenste
Arbeitsschritte
Der Handlingkran Pro von woodtec deckt bei Graz einen Bereich von 10 × 25 m ab; man kann also den ganzen Bereich der Montageplattform und das Materiallager damit bedienen. Der Vakuumheber kann auch großformatige Platten bis 300 kg heben. Mit Balkengreifern kann ein Mann schwere Balken allein auf den Tisch befördern. Und dank des Schnellwechselsystems kann der Vakuumheber gegen eine Einblasplatte eingetauscht werden. Damit geht das Dämmen der Elemente viel schneller vonstatten, und dank des integrierten Schlauchsystems ist man immer gleich fürs Einblasen gerüstet. „Das Wertvolle an dem Portalkran ist sein starres Teleskophubwerk“, ergänzt Graz die Vorteile. Das Scherenhubwerk verhindert das Schwingen der Last, ermöglicht zudem hohe Geschwindigkeiten und punktgenaues Anfahren einer Position.
Die damit verbundenen Zeitgewinne summieren sich über die gesamte Einsatzzeit zu beträchtlichen Einsparungen.
Der Kran lässt sich über eine Fernsteuerung mit stufenlosen Joysticks bedienen. Die Last muss nicht geführt werden, was die Mitarbeiter völlig entlastet und den Arbeitskomfort und die Attraktivität der Vorfertigung deutlich erhöht. Assistenzfunktionen wie Auto-Homing und positionsgerichtetes Fahren sind zusätzliche nützliche Erweiterungen.
Vorfertigung fast gänzlich vom Hallenkran unabhängig
Eine weitere Anwendung ist das Wenden der Elemente mit einem zusätzlichen Wende- und Transportmodul auf dem Handlingkran. Per Fernsteuerung können zwei Haken auf einer Krantraverse gesenkt werden; damit ist man sofort fürs Wenden gerüstet und kann die Elemente auch an eine andere Station weitertransportieren und dort ablegen. Selbst der Hakenabstand ist per Fernsteuerung einstellbar. Damit wird der Hallenkran nur noch zum Abtransport der fertigen Elemente benötigt. Er steht damit wieder vollumfänglich zum Verladen und zur Beschickung der Abbundmaschine zur Verfügung, was die Wartezeiten reduziert hat.
Multifunktionsportal für die Bearbeitung der Beplankung
Zeitgleich zum Handlingkran investierte man bei Graz auch in ein MFP 350 von woodtec. Das Multifunktionsportal ermöglicht ein benutzergesteuertes Abklammern und Ausfräsen der Beplankung ohne vorherige Datenaufbereitung. „Das Portal integriert sich in den bestehenden Zimmermannstisch“, erklärt Graz und sei mit Augenmerk auf den Handwerker konzipiert worden. Ausserdem wurde damit die Investion sehr gering gehalten, und es bot einen guten Einstieg in die Automatisierung der Vorfertigung.
Die Bedienung kann sich jeder Mitarbeiter problemlos aneignen. Per Joystick bewegt der Bediener das Portal und fährt auf diesem mit. Das Portal verfügt über Sensorik und Routinen, um Ständer automatisch abzuklammern, und einen Touchscreen, um die Sprungmaße ab Plan on the fly eingeben zu können. „Beim Abnageln können wir nun Automatikgeräte verwenden“, erklärt Graz. Damit spare man sich das zeitintensive Nachladen, und die Klammerabstände würden immer sauber eingehalten. Das spiegle auch die ständig steigenden Anforderungen wider, gerade im mehrgeschossigen Holzbau.
„Kürzlich forderte der Ingenieur doppelte Klammerreihen mit 30 mm Klammerabständen“, sagt Graz, „da hätten unsere Leute sich ohne Portal und Automatikgeräte komplett wund gescheuert.“
Genauso sei der Einsatz eines Automatikgeräts für große Breitrückenklammern bei Weichfaserplatten top, meint Graz. Das entlaste die Mitarbeiter viel mehr als ursprünglich angenommen.
Zum Ausschneiden der Beplankung können die Maße einfach auf dem Touchscreen eingetippt werden, statt sie auf dem Element anzuzeichnen und dann auszuschneiden. „Die Leute buckeln so viel weniger auf den Knien herum“, meint Graz. Ein wichtiger Grund der Anschaffung war schließlich, den Mitarbeitern attraktive Arbeitsplätze und Arbeitsbedinungen eines modernen Unternehmens bieten zu können.
Der Vorteil der kollaborativen Arbeitsweise, bei der Daten nicht vorher aufbereitet werden müssen, sei nicht nur die reine Zeitersparnis, sondern auch, dass die Mitarbeiter noch selbst etwas bewirken können. Bei woodtec sei man mit dem nächsten Software- Upgrade zwar bereits so weit, dass man auch Daten über .btl einlesen kann. Der Mitarbeiter aber soll jederzeit flexibel eingreifen
und die Prozesse selbst koordinieren können. Ganz nach dem Grunsatz „Zero Labour, Just Work“.
Verkürzte Arbeitsflüsse und eigenständige Arbeitsplätze
Der schrittweise Ausbau der Maschinentechnik ging natürlich auch einher mit dem Umstellen und Optimieren der Arbeitsabläufe und -flüsse. Früher wurde das gesamte Plattenmaterial auf der Striebig vorgängig zugeschnitten und am Montagetisch dann nur noch zusammengebaut. „Mit der neuen Einrichtung verwenden wir nur noch großformatige Plattenwerkstoffe, ob OSB, Gipsfaser-oder Weichfaserplatten“, erklärt Graz. Die Platten werden in Rohgröße direkt neben dem Tisch abgeladen. Dank des Handlingkrans kann ein Mann diese selbst heben und mit dem MFP abklammern und ausfräsen. „Wir haben damit einen sehr zeitaufwendigen Arbeitsschritt und die ganze Logistik rundherum voll eingespart“, erläutert Graz. „Die Großformatplatten reduzieren auch die Zahl der Stöße und damit verbundene Bearbeitungszeiten.“ Wo früher zwei Zimmerleute gemeinsam an einem Element gearbeitet haben, fertigen nun zwei bis drei Leute parallel vor. „Sie teilen sich Handlingkran und Multifunktionsportal, können auch mal gemeinsam aushelfen, aber sind dank des selbstständigen Arbeitens viel rationeller unterwegs“, erklärt Graz. Und der Anreiz, auf eingängige, komfortable, technikgestützte Weise ein gesamtes Element in voller Ausbaustufe selbst zufertigen, biete eine spannende Herausforderung.